Double-layer sintered wire mesh is a popular type of stainless steel mesh used for filtration and aeration applications.
When we talk about single-layer sintered wire mesh, it’s important to note that it doesn’t unravel or let wires move around when cut, rubbed, folded, or creased. The shape and size of the mesh’s holes stay the same because the wires are fused together, making the mesh a solid piece.
Double-layer sintered wire mesh for better performance
Double-layer sintered wire mesh retains the same characteristics as the single-layer version, while also combining the benefits of a dual-layer design for enhanced overall performance. This improved performance is often seen in its strength. One layer serves as the primary working surface, while the other acts as a supportive or reinforcing layer.
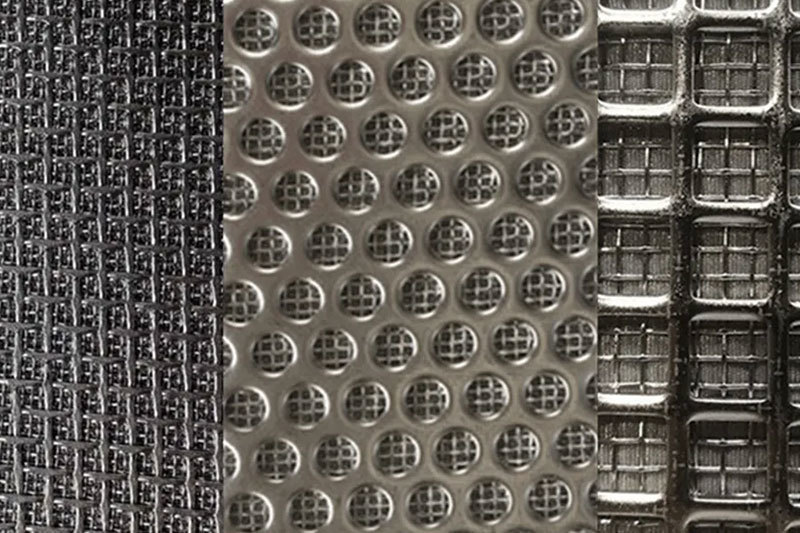
Double-layer sintered wire mesh for higher strength
The top layer is usually a fine square weave mesh or Dutch weave filter mesh, which is typically thin and not strong enough on its own to create a tube or disc shape. The bottom layer can be a coarse square weave mesh or a perforated metal sheet. The coarse square weave mesh has large openings and is lightweight. A perforated metal sheet is very versatile, with options for hole size, shape, pattern, openness, and thickness. It’s an excellent choice for applications requiring high pressure, such as disc filters and strainer filters.
Double-layer sintered wire mesh for pore distribution
Another combined performance of the two layer sintered wire mesh is changing the flow direction through the filter media. One typical application is the type D sintered mesh for fluidizing bed. 2 layer of Dutch weave filter mesh is aligned with 90 degree difference. The flow path is converted and distributed into a uniform diffusing way.